ミニセミナー・基礎講座
リソグラフィ
フォトレジスト
リソグラフィによる高分子パターン形成
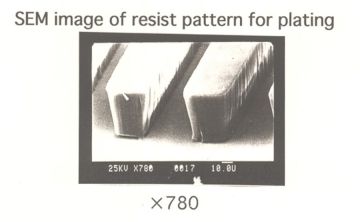
電子デバイスの発展とともに、シリコン材料を主体とした微細加工技術(リソグラフィ)が進展してきた。基板のエッチングには、高分子材料を主体としたマスクが用いられる。超LSIデバイス(高集積半導体素子)用のリソグラフィ技術として、X線、電子線、イオンビーム等が注目されてきた。しかし、最近、紫外線によるリソグラフィ技術の発展が目ざましい。
右図(1)は、回路基板に多用されるDFR(ドライフィルムレジスト)の現像後の電子顕微鏡(SEM)写真である。これらのレジストパターン形成には、レジスト材料、露光技術、現像技術、表面処理技術などの多くの技術が集積することで、確実に、かつ安定して実現できる。下図は、レジストパターンの幅と高さの寸法を基準にしてまとめた技術トレンドである。通常、解像度の指標としてパターン線幅が多く用いられるが、パターン形成の観点からは、パターン高さを考慮したアスペクト比(=高さ/幅)が重要となる。下図において、アスペクト比が増加する左上の方向が技術革新を意味する。
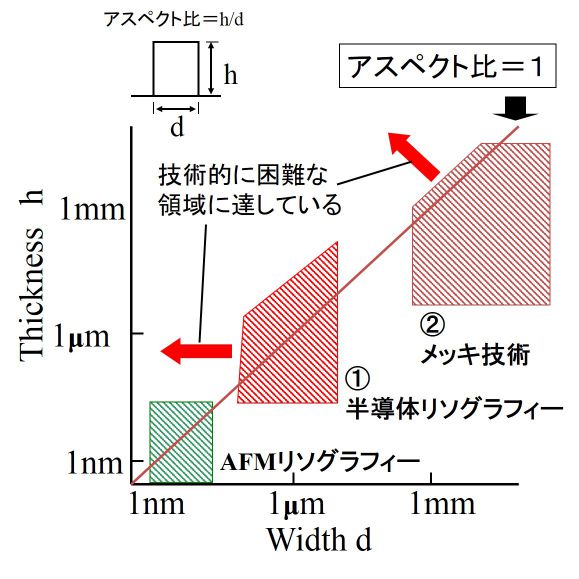
下図に、光リソグラフィの代表的なプロセスフローを示している。光リソグラフィ技術は、マスク上に形成されたLSIの各層毎の回路パターンを、高圧水銀灯による紫外光(λ=200~500nm)を用い高分子膜に焼き付けるものである。このプロセスは、(1)基板形成、(2)密着強化処理、(3)高分子膜塗布及びソフトベーク、(4)露光、(5)現像、(6)DUV(Deep Ultra Violet)光照射とハードベーク、(7)基板エッチング、(8)高分子膜除去の工程に分けることができ、この順序で基本的に半導体基板を処理していく。また、レジスト材料にはポジ型とネガ型があるが、厚膜やフィルム化が容易である理由から、回路基板ではネガ型を用いる場合が多い。ネガ型レジストの特長は、図(1)のようにパターン上部の線幅が太い逆テーパー型になることである。最近では、厚膜のポジ型レジストも登場し実用化が進んでいる。
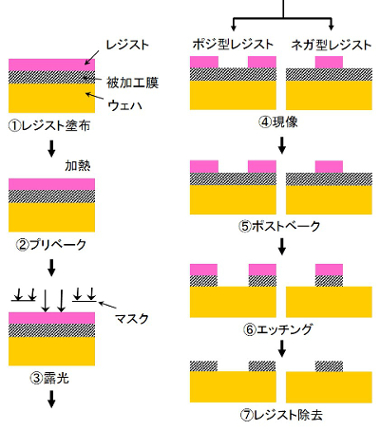
(1)基板形成
LSIに用いられる無機膜にはSiO2,Wsi2など約15種類があり、CVD(Chemical vapor deposition)、スッパタリング、熱酸化法等で形成する。膜厚はほぼ0.01~1μmの範囲であり、これらの膜は、数100~1000℃以上の熱履歴を有している。回路基板には、ガラエポやポリイミド、あるいは5G対応のフッ素樹脂などの多種多様な材料が用いられる。その上に、配線材料としてCu膜がメッキ等で形成される。あるいは一面のCu膜を形成して、レジストマスクに従ってエッチング除去する場合もある。基盤樹脂には、低誘電率性および低誘電正接が求められる。
(2)密着強化処理
これは、高分子膜を塗布する前に基板表面を十分乾燥・疎水化させて、塗布むらや現像・エッチング時の高分子膜剥がれを防止する目的をもつ。これには、200℃以上の熱処理を行ったり、HMDS(Hexa-methyl-disilazane)といったシランカップリング剤を用いて蒸発塗布したりする。
(3)高分子膜塗布、ソフトベーク
回路基板に用いられるレジスト材料には、ドライフィルム(DFR)が多く、ラミネートにより基板上に均一にシートを形成する。また、高分子膜は樹脂、感光剤およびそれらを溶解している有機溶剤から成っている。Si基板上に高分子溶液を滴下し、スピナーという回転式塗布機を使って3000~6000rpmで高速回転させると、高分子膜は均一な膜になって基板上に残る。通常、厚さは1μm前後になる。その後、高分子膜中から溶媒を揮発させるため、90℃前後の比較的低温で熱処理を行う。これをソフトベークという。
(4)露光
作製したい電子回路(どの位置にp型領域を作るかなど)パターンを、石英板上にクロム膜で形成したフォトマスクを用いて紫外線で露光する。露光機として、回路パターンを5分の1に縮小させる縮小投影露光機(ステッパー)を用いる。代表的な国内メーカーとしてASML、ニコン、キヤノンがある。最近では、DMD(ディジタルミラーデバイス)により、マスクレスで回路パターンを露光する技術も実用化されている。
(5)現像
これは、紫外線照射によって高分子膜中に形成された潜像を顕在化させるプロセスである。現像液には、通常TMAH(Tetramethylammoniumhydrooxide)2.38%水溶液といった強アルカリ(pH12)溶液を用いる。ポジ型高分子膜では、露光部が現像時に除去される。現像は、露光部と未露光部の溶解速度の差を利用してパターンを得ようとするプロセスである。現像後には、純水によりリンス処理が行われる。
(6)DUV照射、ハードベーク
ハードベークは、現像によって形成された高分子パターンを焼き締めるためのものである。現像後の高分子中には未揮発の有機溶剤や未硬化部分が残っているため、100~150℃前後で熱処理を行う。それによって、エッチング耐性が向上する。また、耐熱性の良くない高分子膜、または150℃以上の高温ベークでは、高分子膜が熱だれを起こしパターン形状が劣化する。そのため、ハードベークの前にDUV光(λ=200~300nm)を照射し、高分子膜表面を硬化させて熱だれを防止する。
(7)基板エッチング
作製した高分子パターンをマスクにして基板のエッチングを行う。エッチングにはドライとウェットの2種類がある。ドライエッチングは、エッチングする基板の種類に応じてCF4やCCl4などの反応性ガスを選択する。エッチング時の高分子パターンの膜べりと基板材料の膜べりの差を利用して、基板加工を行う。この膜べりの比を選択比と定義する。また、SiやSiO2基板に対してはウエットエッチングには異方性エッチング用のEPW水溶液やフッ化水素酸が用いられる。
(8)高分子膜除去
エッチング後の高分子膜は、酸素プラズマあるいは有機溶剤を用いて基板より除去される。近年では、このレジスト除去の高精度化が求められている。
以上で、光リソグラフィによるパターン形成プロセスが完了する。
これらのパターン形成において、感度曲線が最適化の基本となる。下図はレジストプロセスにおける感度曲線を表している。横軸は露光量、縦軸は現像後のレジスト膜の残膜率(規格化)を示している。ポジ型レジストの場合、露光量は増加するが膜厚は減少しない。感光剤と樹脂とは溶解阻止効果があり、露光量が低い場合は、現像液への溶解性を殆ど有していない。露光量が増加し、しきい値(Eth)に近くなると膜厚は急激に減少する。この時の傾きをコントラストと定義され、レジストパターンの断面形状に大きく影響する指標となる。ネガ型の場合は、これらの逆の性質を有する。

DFRレジストによるメッキプロセス
下図は、ドライフィルムレジスト(DFR)を用いて、メッキによる回路パターン形成を示している。DFRパターンに沿って、均一な金属メッキ膜が形成されていることが分かる。DFRには、メッキ中の金属の強い凝集性に耐える特性が求められる。また、基板とDFR界面での寸法変形等が無いことが必要である。
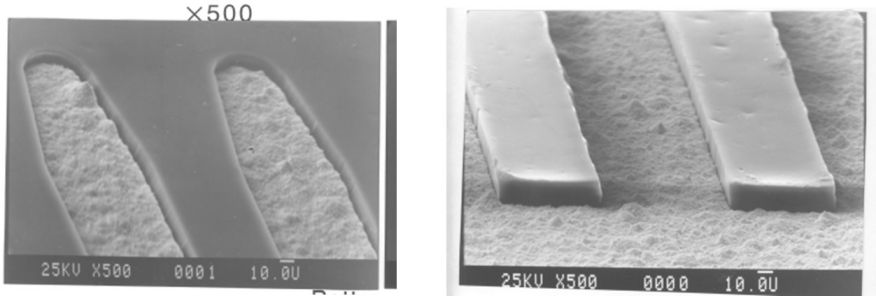
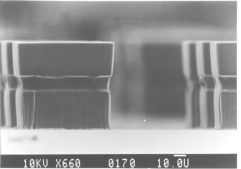
下図は基板とDFR界面にメッキ液が浸透したことによる不良を示している。これらの不良は回路ショートなどのトラブルを引き起こす原因となる。形状コントロールとしては、右図のように、積層プロセスにより形成したパターンを示している。DFRを用いた場合、溶剤系のレジストコーティングと異なり層間の溶剤ミキシングが生じない。また、レジストパターンの断面形状コントロールが可能であるなどのメリットがある。パターン解像力は高くないが、今後のIoT分野に対応できるDFR積層プロセスとして注目されている。
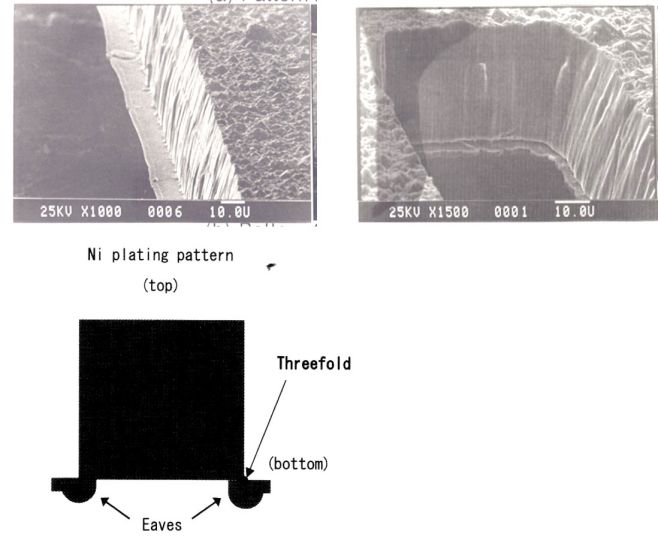
塗膜ラインパターンは先端から剥離する
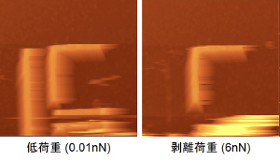
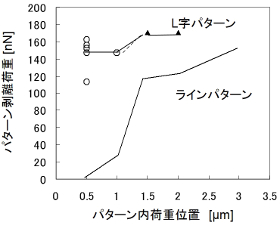
電子デバイス回路に用いられる微細レジストパターン形状は、設計手法の高機能化に伴って複雑である。レジストパターンの単位面積あたりの付着エネルギーは同一であっても、パターン形状の違いによって剥離挙動が異なる。よって、パターン形状に依存した応力分布に注目し付着力を解析する。まず、右の上図は、KrFエキシマレジストパターンのAFM像を示している。これらのパターンの線幅は170nmであり、L型とラインの2種類である。ここで、AFM探針を用いて、それぞれのパターン端から位置を移動させて荷重を加える。破壊後のパターン像も示している。右の下図は、各パターンにおける荷重位置と剥離荷重の関係を示している。パターン端部では、L型パターンの方がラインパターンに比べて付着強度が高い。しかし、荷重位置がパターン端から離れるにつれて、剥離荷重は等しくなり、パターン形状の差が無くなる。これは、各パターン内に生じる応力分布の違いに起因する。すなわち、下図のように、荷重位置が同一であっても、ラインパターンよりもL字パターンの方が、レジスト/基板界面での応力集中が緩和されている。また、荷重位置がパターン端部から離れた場合、界面付近の応力値はパターン形状に依存しなくなる。よって、AFM測定と応力解析の組合せにより、レジストパターンの付着力の形状依存性が説明できる。

以上のように、AFMの微細探針を用いて荷重を加えるDPAT法により、微細レジストパターンの付着力解析を定量的に解析することができる。一般に、凝集性の低い高分子材料の微小固体の研究には、AFMなどの精密な制御システムが必要になる。本手法によれば、レジストパターンだけでなく、微粒子やナノ構造体の付着凝集性の解析も可能である。AFMを用いることにより、溶液中での付着挙動解析も可能となり、付着界面への溶液の浸透性の解析に有効である。
参考文献
- 河合 晃, "原子間力顕微鏡(AFM)を用いた微細探針走査法によるフォトレジスト微細パターンの接着性解析", 日本接着学会誌, 36, 2-9 (2000).
微細加工パターンの付着性と付着面積
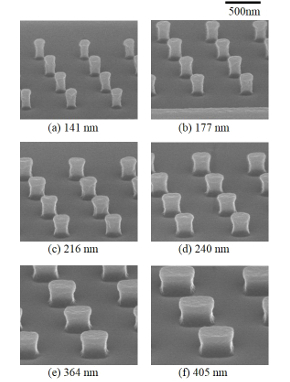
レジストパターンの付着力のサイズ依存性を解析するために、右図にあるようなドット形状の化学増幅型レジストを用いた。測定に用いたパターンのサイズ(直径)は、141~405nmの範囲である。パターンの一部にAFMの探針を接触させて荷重を加えて、剥離に必要な荷重を求める。下の左図には、これらのパターン付着力のサイズ依存性を示している。サイズの縮小に伴って、付着力が減少している。これは、基板とレジストパターン間の付着面積の減少が主な要因である。パターンサイズが250nmより細くなると極端に付着力が減少する。これは、探針からの荷重によって、レジストパターン内の応力分布に違いが生じたためである。すなわち、サイズが250nmより太い範囲では、倒壊時の応力はレジストと基板との界面に集中するが、それよりも細いパターンでは、界面より少し上部に応力が集中する。よって、250nmよりも細いパターンでは、容易に凝集破壊が生じて剥離荷重も低くなる。しかし、250nmよりも太いパターンでは、界面付着力は高く剥離は生じない。これらの結果は、パターン剥離後に基板上に形成される残渣の有無と対応する。
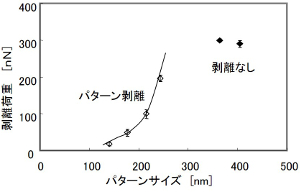
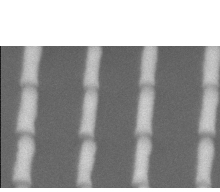
さらに、レジストパターンのサイズ依存性について検討する。試験パターンとして、上の右図のような円柱形のレジストパターンを用いる下図は、DPAT法による剥離荷重とパターン直径との相関を示している。パターンサイズの縮小に伴い、レジストパターンは剥離しやすくなる。また、この剥離性は、パターンの断面積に比例しているため、レジストパターンと基板界面での接触面積およびパターン断面の凝集力に依存している。以上のように、ナノスケールでの固体の凝集性を直接解析する手法として、DPAT法は有効である。
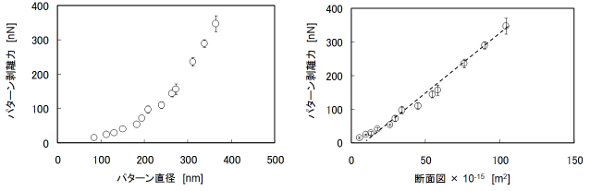
参考文献
- Akira Kawai, "Analysis of Pattern Collapse of ArF Excimer Laser Resist by Direct Peeling Method with Atomic Force Microscope Tip", Microelectronic Engineering, vol.57-58, pp683-692 (2001).
- Akira Kawai, "Adhesion and Cohesion Properties of Dot Resist Patterns Ranging from 84 to 364 nm Diameter Analyzed by Direct Peeling Method with Atomic Force Microscope Tip", J. Photopolymer & Science Technology, 15, 121-126 (2002).
- Akira Kawai, "Adhesion and Cohesion Analysis of ArF/SOR Resist Patterns with Microtip of Atomic Force Microscope (AFM)", J. Photopolymer Science and Technology, 14, 507-512 (2001).
溶液中の塗膜パターンの付着力
におけるレジストパターンの付着力
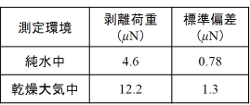
AFMを用いた物性解析の特長の一つとして、溶液中における固体の付着力解析がある。これにより、ウェットプロセス中での付着挙動解析が可能となり、この手法の適用範囲が大幅に広がる。レジストパターンの剥離は、パターン現像プロセスの純水リンス中で生じていることから、溶液中での付着力測定が必要になる。そこで、下図にあるように、AFMを用いて、純水中でのレジストパターンの付着力解析を行う。測定環境が液体中であること以外は、同様の操作でパターン剥離を行う。結果として、右表にあるように、純水中のパターン剥離荷重は、大気中に比べて約1/30に低下する。これは、レジストと基板界面への純水の浸透力によって、パターン剥離が促進されたためである。溶液の浸透エネルギーは、付着エネルギーよりも1割程度低い値であり、純水中ではレジストパターンは辛うじて基板に付着している。この状態で探針から荷重を加えると、レジストパターンは容易に基板から剥離する。このように、AFMを用いることで、様々な環境における微小凝集体の付着挙動をin-situで定量的に解析できる。
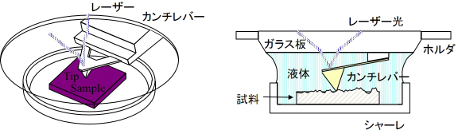
高分子パターンと微細空孔(vacancy)
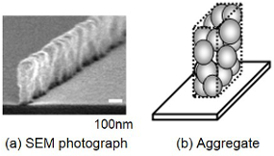
付着性の解析において、付着界面の情報を直接得ることは重要となる。しかし、通常、付着界面の情報を得ることは困難である。ここでは、AFMを用いて、微細パターンと基板との付着界面を直接観察する。右図はギガビットクラスの最先端LSIの製造に使用される60nm線幅の高分子パターンである。主成分はスチレン系樹脂である。高分子パターンの表面には、ナノスケールの細かな凹凸が存在する。これは、高分子パターン内に、20~30nmの大きさの高分子集合体が凝集していることに起因する。エッチング用マスクとして高分子パターンを用いた場合、この微細凹凸が加工精度に大きく影響する。この表面の凹凸は、付着界面にも影響すると考えられる。下図は、AFM探針を用いて、基板上のパターンを剥離し、付着界面を直接解析する手法を示している。AFMを用いることで、パターン上の特定の箇所を剥離することが可能となる。この技術により、高分子パターンと基板界面との付着状況を知ることができる。
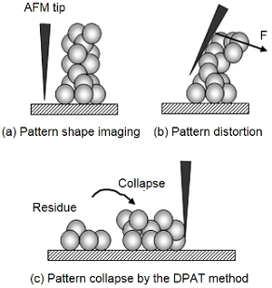
下図は、AFMを用いて、線幅60nmのラインパターンを、広範囲に剥離して付着界面の状態を示した像である。界面には、高分子集合体が1個抜けた空孔(vacancy)が点在する様子が明らかに観察できる。この空孔は、パターン長さ1μmあたりに1個の割合で存在するため、デバイス製造の面からは高い頻度となる。また、この空孔はパターンの付着力に寄与せず、逆に、この空孔に応力集中が生じ付着上不利になると考えられる。このように、AFMを用いることで、ナノスケールでの付着界面の状態を明らかにできる。
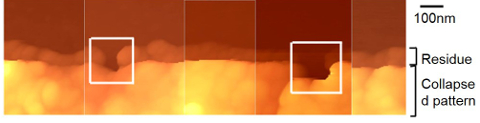
レジストパターン内の屈折率分布測定
光リソグラフィ技術により作製されたレジストパターンの側面には、110~180nm程度の周期の波形模様が形成される。この波形模様は、パターン露光時の定在波効果に起因して形成される。原子間力顕微鏡(AFM)を用いて、直径0.61μm、高さ1.03μmの円筒形レジストパターンを基板上で剥離倒壊させて、パターン側面に形成された波形模様を観察した。波形模様の周期はパターン側面内で異なることより、レジストパターンの高さ方向の屈折率分布を求めた。その結果、屈折率は1.51~1.79の範囲で、パターン上部から底部へ向けて徐々に高くなっていることが分かった。これは、ホットプレートを用いた熱処理により、レジストパターン底部の凝集性が高くなったことを反映していると考えられる。この手法により、微小固体中の光学パラメータおよび凝集性を解析することが可能になる。
実験に用いたレジストの主成分は、m-クレゾール/p-クレゾール/キシレノール/ホルムアミドノボラック樹脂である。溶剤はECA(エチルセルソルブアセテート)である。レジストパターンの形成方法は以下の通りである。まず、スピンコート法により、レジスト膜をSi(100)単結晶基板上に形成した。スピンコートしたレジスト膜を乾燥させる目的で、ホットプレートを用いて100℃で1分間の熱処理を行った。その後、縮小投影露光装置(Nikon、NSR1505-G6E、g-line、NA=0.54)を用いて、300msecの露光時間で直径610nmのパターン形状の露光を行った。露光波長は365nm(i線)であった。パターン露光時には、定在波効果によって、レジスト膜の深さ方向に光学強度の周期的な濃淡が形成される。これは、後述のように、レジスト膜内で、入射光と基板からの反射光が干渉するために生じる。その後、レジストパターンをTMAH(テトラメチルアンモニウムハイドロオキサイド)2.38%水溶液中に漬けて、1分間の現像処理を行った。引き続き、純水中で1分間のリンス処理を行った。パターン現像とリンス処理時の環境温度は25℃であった。パターン側面に形成された波形模様は、AFM(SPA300、セイコー電子工業(株)製)、および走査型電子顕微鏡(SEM、JSM-35CFⅡ 日本電子(株)製)により観察した。AFMによる測定手法および条件は、以下の通りである。まず、本手法では、レジストパターンをDPAT法により剥離倒壊させて、パターン側面の波形模様を観察する。測定には、Si3N4製のカンチレバーを使用した。カンチレバーの先端には、AuコートしたSi3N4製の探針が取りつけられている。カンチレバーのバネ定数および探針先端の曲率半径は、それぞれ0.098N/mおよび20nmであった。探針からパターンへ加えた荷重は、カンチレバーの変位とバネ定数を掛けることで求まる。図1は、AFMによるパターン側面形状の解析方法を示している。まず、AFMのコンタクトモードにより、0.01nNの低荷重下でパターン観察を行う。この荷重下では、パターン変形および剥離は生じない。そして、レジストパターン上部の角に30nNの荷重を加えることでパターンを倒壊させる(図1a)。最後に、剥離倒壊したパターンの側面形状をコンタクトモードにより精密に測定する(図1b)。
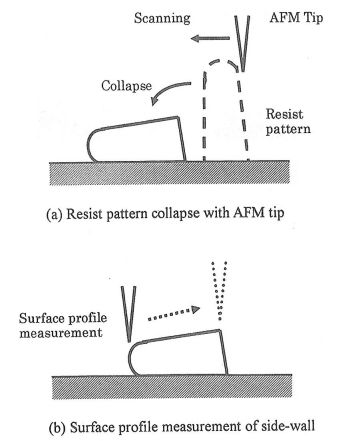
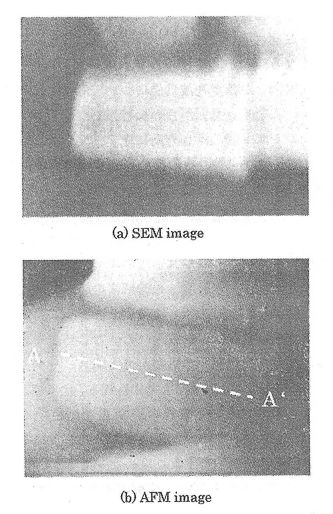
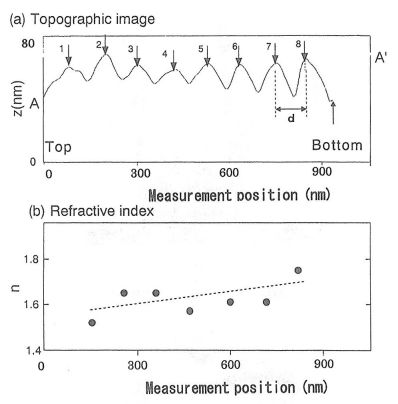
AFM像の中からパターンを1つ選択して、図1で示したように、荷重を加えて剥離倒壊させる。図2には、倒壊後のレジストパターンのSEMおよびAFM像をそれぞれ示している。両者ともパターン側面に波型模様が確認できる。そして、図3aには図2bのAFM像のA-A’面での断面形状プロファイルを示す。波形模様はパターン上部から底部にかけて形成されているが、その周期と深さは僅かに変化していることが分かる。特に、パターン底部に近いほど周期が短くなり、かつ、その凸凹は大きくなる傾向がある。ここで、パターン側面の波型模様の形成要因となる定在波効果について考察する。定在波効果とは、入射光と基板からの反射光とがレジスト膜中で干渉し、レジスト膜の深さ方向に光学強度の濃淡が周期的に生じることである。その場合の光学強度の濃度変化の周期T(nm)は、下式で表すことができる。
T=λ/2n
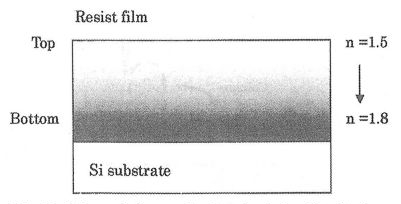
ここで、λ(nm)は入射光の波長、nは波長λにおけるレジストの屈折率である。レジスト膜の場合、深さ方向の光学強度の濃度変化が、現像液への溶解度の差として反映される。その結果、図2および図3aのような周期的な波形模様がパターン側面に形成される。ここで、もし、レジスト膜の深さ方向に屈折率分布がある場合、パターン側面の波形模様の周期も変化すると考えられる。よって、パターン側面に形成された波形模様の周期Tを測定することによって、レジストパターン内の屈折率分布を求めることができる。図3bは上式より求めたレジストパターン内の屈折率分布を示している。屈折率の値は1.51から1.79の範囲内で変化しており、最小自乗曲線から分かるように。パターン上部より底部の方が高くなっている。これは、図4のように、スピンコート法で形成したレジスト膜において、基板との界面付近の屈折率は、膜表面よりも高いことを示している。また、図3bより、波形模様の深さはパターン底部に近いほど高くなっているため、露光時の定在波効果もパターン底部の方が顕著である。これは、レジスト膜表面よりも、基板近傍の反射光強度が高くなるためである。
ここで、レジストパターンの屈折率変化と凝集性との関係について考察する。一般に、物質の屈折率nは、誘電率εと密接な関係がある。これらは、下式のクラウジウス-モソッテイの式として、単位体積当たりの分子数(分子濃度)Nおよび分極率αの関数として表わされる。
この式において、ΣNα<3ε0の範囲で解が得られるため、屈折率nおよび誘電率εはΣNα項の増加関数となる。すなわち、レジスト膜の屈折率nの増加は、レジスト内の分子濃度Nあるいは分子分極率αの増加に起因することが分かる。また、本研究では、スピンコート後のレジスト膜に100℃の熱処理を行っている。しかし、レジスト樹脂のクロスリンクは通常約200℃以上で顕著になることが分かっている。よって、レジスト膜の分子構造に起因する分極率αは、100℃の熱処理では殆ど変化していないと考えられる。一方、熱処理による溶剤蒸発により、レジストパターン内の残留溶剤の濃度分布が変化したと考えられる。これは、レジスト膜の熱処理にホットプレートを用いたため、レジスト膜が底部から加熱されて溶剤蒸発が生じることが予測される。すなわち、パターン底部は、パターン上部に比べて残留溶剤量が少なく、それに伴い、パターンの体積収縮も大きくなると考えられる。よって、パターン底部では、レジスト内の単位体積当たりの分子数Nが増加すると考えられる。すなわち、図4のように、レジスト膜内には深さ方向に屈折率分布が生じていると考えられる。よって、現像後のパターン内にも同様の屈折率変化が生じていることが分かる。このように、本手法によれば、レジストパターン内の凝集特性が解析できる。また、微小固体中の屈折率分布を決定できることから、フォトニクス材料のような機能素子の光学解析を解析できる。
薄膜の加工技術とが半導体集積回路の発展
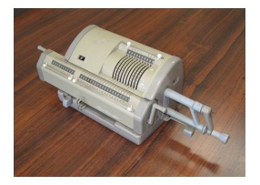
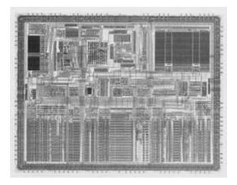
コンピュータの進歩は目覚ましく、インターネット等のIT技術の発展に伴い、私たちの生活に欠かせないものとなっている。今では一人ひとりが携帯用コンピュータを所有し、いつどこでも必要な情報を得るとともに発信することができる。コンピュータの歴史は長く、長年改良を何度も繰り返して現在の高性能を実現している。最初に普及したコンピュータ(計算機)は、上の左図のような多数の歯車の組み合わせを利用した回転式計算機であった。また、この計算機の主な機能は四則演算であった。初期のころは、写真のようにハンドルで歯車を回転させていたが、その後、電動機で回転させる機構に改良された。そのため、計算機という単語には「機」という語が用いられている。現在の最先端のコンピュータも多くの電子部品から構成されている。コンピュータの進歩には、上の右図のようなLSI(Large Scale Integrated circuit)と呼ばれる集積回路素子の技術が大きく貢献してきた。コンピュータに使用されるLSIには、CPU(central processing unit)という演算を主体とするものと、RAM(random access memory)やROM(read only memory)と呼ばれる情報を記憶するメモリ素子とがある。計算時には、多くのデータのやり取りを行うため、CPUやメモリの動作速度が計算速度に大きく影響する。このLSIは多くの微細なトランジスタから構成されている。トランジスタは1948年にショックレーらによって発明された。当時はゲルマニウムという半導体の単結晶に針電極を接触させた構造であった。その後、世界中の研究者が改良を重ねて、トランジスタの革新的な実用化技術が次々と誕生した。現在、トランジスタの誕生から約60年が過ぎたが、コンピュータの飛躍的な発展とともに世の中が大きく変化した。コンピュータの計算方式は、1と0の信号を扱う2進数で構成されている。この2進数の機能は、下の左図のようなインバータとよばれるトランジスタ回路によって実現されている。インバータ回路を用いることで、トランジスタ回路をONとOFFを制御するスイッチとして動作させることができる。実際のLSIに用いられるトランジスタは、下の右図のようなMOS(metal oxide semiconductor)型トランジスタが主流となっている。MOS型トランジスタは、ソース(source)とドレイン(drain)と呼ばれる電極と、その中間に位置するゲート(gate)電極で構成されている。MOSとは、トランジスタのゲート部が、金属(meta)-酸化膜(oxide)-半導体(semiconductor)の積層構造を有していることを意味している。
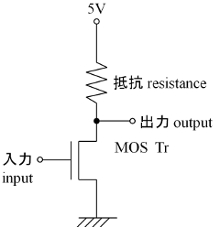
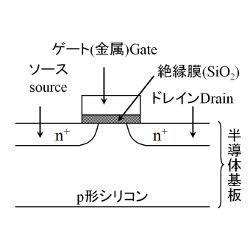
通常、MOSトランジスタの半導体基板にはシリコン単結晶が用いられる。MOSトランジスタの動作時には、下の左図のようにソースから放出された電子が、ゲート下のチャネルを通過してドレインに到達するが、これをゲート電圧によって制御する。よって、チャネル内の電子の移動速度がトランジスタのONとOFFとの切り替え速度を決定する。このチャネルの幅は年々短くなり、現在の最先端のトランジスタでは28nm以下となっている。1ナノメータ(nm)は、10億分の1メートルを表す。よって、MOSトランジスタのサイズが小さいほど、高速にスイッチング動作できる。このように、コンピュータの高速化には、LSIを構成するトランジスタサイズの縮小化が大きく貢献するが、このためにはトランジスタを作製する微細加工技術の進歩が大きい鍵となる。一方、1チップのLSIに含まれるトランジスタ数が増加すると、LSIの消費電力も増加する。消費電力の増加に伴いLSIの発熱が顕著になる。やがて、最終的には動作不良を引き起こす可能性が高くなる。よって、LSI素子開発の歴史において、この発熱対策は重要な技術課題となってきた。その中で、CMOS(complementary MOS)インバータという新たな素子構造が開発された。このインバータの素子構造は下の右図に示すとおりである。この回路は、入力信号に対するスイッチング動作が互いに逆となるように、2個のトランジスタを直列に接続した構造となっている。トランジスタには、ゲート下のチャネルを電子が通過するNMOSトランジスタと、正孔(ホール)が通過するPMOSトランジスタで構成されている。CMOSトランジスタの動作時には、常に片方のトランジスタがOFFとなっているため、回路を通じて電流が流れないため消費電力(損失)がとても少ないことが特徴である。(上の右図の1個のNMOSトランジスタの場合は、トランジスタがONしている間は回路に電流が流れてしまい損失の原因となっていた。)よって、CMOSトランジスタによるインバータ回路を採用することで、高集積で消費電力が少なく、かつ、寿命の長いスイッチング素子が実現できるようになりった。よって、CMOSトランジスタの登場により、コンピュータの高速化と低消費電力化が達成され、現在のような大幅な進歩を達成することができた。
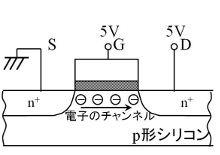

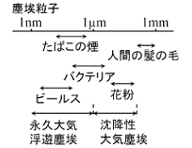
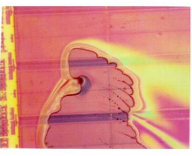
(微粒子と塗布むら)
トランジスタサイズの縮小化には、ナノテクノロジーにおける最先端の製造装置が多数使われる。具体的にはリソグラフィといった縮小投影露光装置や、ドライエッチング、CVDなどの多くの高価な精密装置が使用される。しかし、トランジスタの微細化を推進する上で様々な課題を抱えている。その一つに微小欠陥による製品不良がある。右の上図は、身近な微細欠陥をサイズについてまとめている。大気中には、ウィルスやたばこの煙のような1ミクロン以下の微小固体や、花粉などの数10ミクロンサイズの微粒子が存在する。1ミクロン以下の微粒子は永久性浮遊塵挨と呼ばれ、地上に落下することなく大気中を漂う。また、1ミクロン以上の欠陥は、時間が経てば落下する沈降性浮遊塵挨と呼ばれる。これらの塵挨は、LSIの製造過程で半導体チップ上に付着することで、欠陥製品を生み出してしまう。右の下図は、実際に半導体チップ上に付着した微小欠陥の写真を示している。この欠陥のサイズは約10ミクロンであり、欠陥が原因となって、処理液の塗布むらを引き起こしている様子が分かる。通常、肉眼では約40ミクロンまでが認識できる限界であるため、これらの微細欠陥は光学顕微鏡を用いて観察する。この欠陥がLSI基板上に存在すると、トランジスタは動作しなくなるため、下の左図のようなクリーンルームが必要になる。クリーンルーム内では、天井からヘパフィルターを通過した清浄なエアーを噴き出して循環している。そのため、クリーンルーム内では、机上に置いた鏡には1年間経っても埃が付着しない。また、下の右図のように、クリーンルーム内では、作業者もクリーンウェアを着て埃を出さないようにしている。クリーンルーム内での主な発塵源は、人間の衣類や汗などが第一原因である。よって、最先端のクリーンルームでは、作業者が一人もおらず、全て自動ロボットが製造作業をしている。このようにして、LSI製造中のクリーン度を維持しながら、真空装置を用いたドライプロセスや、ウェットプロセスなどの様々な機器を使用する。このように微細加工技術を駆使して、CMOSトランジスタを搭載したLSIは完成する。
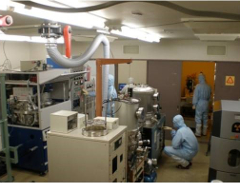
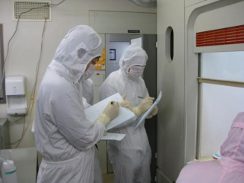
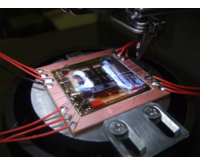
将来のコンピュータには計算機能だけではなく、身近な信号源を多く取り入れたインテリジェントな制御が期待されている。最近では、センサや駆動機構などの新機能を有したコンピュータが登場している。よく知られているように、車のエアーバック、全方位センサ、ゲーム機用のセンサなどが実用化されている。これらは、微小電子機械(MEMS: micro electronic mechanical systems)と呼ばれるインテリジェントな電子デバイスに分類にされる。具体例として、下図は、ガスや液体などの流体を制御できるマイクロポンプデバイスの基本構造を示している。デバイスの中の複数の円形ダイヤフラムが振動して、流体を送り出す機構を有している。これはLSIの発熱対策の一つとして、循環ガスで冷却する機能として期待されている。右図は実際のマイクロポンプデバイスの写真である。これらのデバイスは、クリーンルーム内の製造装置を用いて約1カ月の期間で作製できる。将来的には、ロボット産業の発展に伴い、様々な信号源に対して柔軟に処理できるLSIや、自律的に状況判断を行う電子デバイスが求められている。今後もLSIの多機能化がさらに進むことで、インテリジェントな次世代コンピュータの登場が期待される。
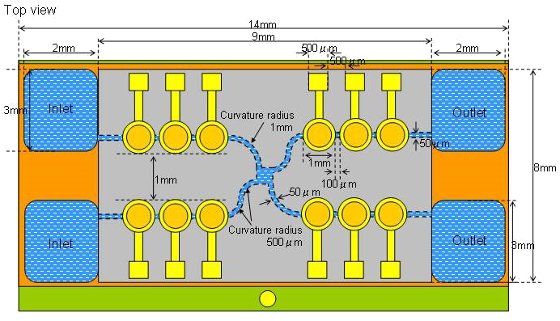
最先端エレクトロニクスへの塗膜技術
近年、MEMS(Micro Electro Mechanical Systems, 微小電子機械素子)は、自動車のエアバッグやゲーム機などの主要な部品である加速度センサが相当し、センサ、制御機器、バイオ分野などで目覚しく発展している。MEMSの作製には、有機無機の多くの薄膜が用いられている。また、バルク体を薄膜化するダイヤフラム薄膜も多く用いられている。ここでは、ダイヤフラム薄膜の作製プロセス、および制御技術について述べるとともに、ダイヤフラム型流体制御MEMSの動作原理について紹介する。
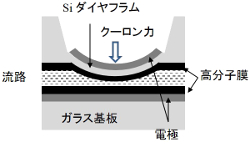
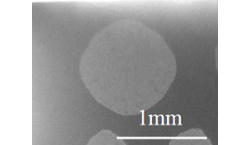
上の左図はマイクロダイヤフラムの断面構造を示している。材質はシリコン(Si)であり、ダイヤフラムの直径は1mm、厚さは30ミクロンである。このダイヤフラムはSi単結晶のウェットエッチングにより形成する。ダイヤフラムの上面にはAu電極膜が形成されている。また、ダイヤフラムの下面には、ポリマー膜がコートされている。ダイヤフラムはマイクロチャネル(流路)に接続されており、流体の流れを制御できる機構を有している。チャネルの幅は50ミクロンである。これらは光リソグラフィ技術で作製する。制御する流体として、液体やガスなどが選択できる。特に、反応性や腐食性のある流体に適用可能である。このダイヤフラムは繰り返し動作させるため、繰り返し疲労耐性が求められる。上の右図は、マイクロダイヤフラムの形成後の顕微鏡写真である。ダイヤフラムの表面は、平坦であることが確認できる。
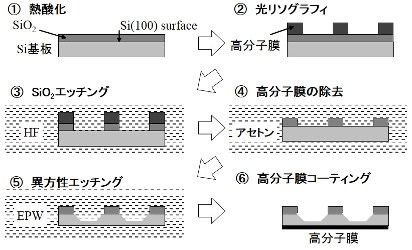
上図は、Si製のマイクロダイヤフラムの形成フローを示している。最初に、Si基板表面にエッチングマスクとなるSiO2膜を形成する。SiO2膜の膜厚は45nm程度であり、電気炉を用いた熱酸化法で形成する。次に、高分子膜によるダイヤフラムの形状パターンを、光リソグラフィ法で形成する。これはSiO2膜のエッチングマスクとなる。そして、HFF水溶液に浸漬することにより、SiO2膜を溶解除去する。その後、アセトンなどの有機溶剤等により、マスク材料であった高分子膜を溶解除去する。Si基板は、SiO2パターンをマスクとして、開口部を所望の深さにまで溶解する。この際、エッチング溶液には通常EPW溶液を用いる。そして、SiO2膜をHF水溶液中で除去する。以上のプロセスで所望の膜厚にダイヤフラム膜を制御できる。最終的に、制御用の金属電極膜や高分子膜をコーティングして、マイクロダイヤフラムが完成する。
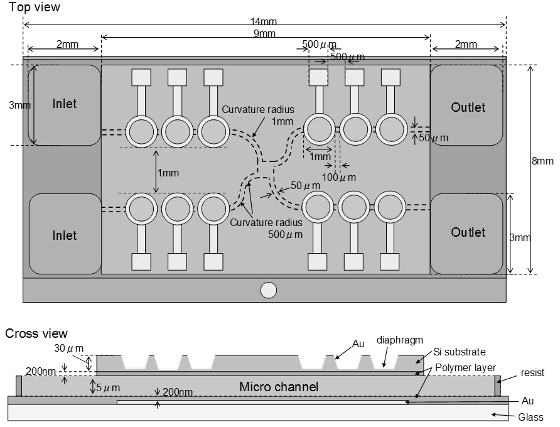
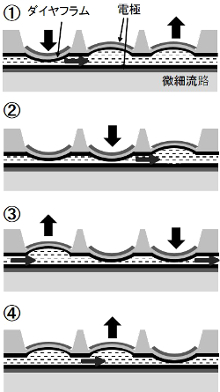
上図は、これらのダイヤフラムを搭載した流体制御MEMSのデザイン図である。中央部に円形の12個のダイヤフラムが確認できる。各ダイヤフラムには、電圧印加用の配線が接続されている。また、デバイスの左端には流体供給口、右端には流出口が設けられている。供給口は2系統あり、流出口も2系統である。各ダイヤフラムはマイクロチャネルで結合されている。3個が一つのブロックを形成し、4ブロックに分けられている。中央部でチャネルは交差しており、流入した2種類の流体を混合・分離制御することが可能である。右図は、1つのブロックを構成する3個のダイヤフラムの動作シーケンスを示している。①:左端のダイヤフラムは圧縮し、流体を押し出す。その際、右端のダイヤフラムは拡張し流体を吸入する。②:中央のダイヤフラムが圧縮し、右側へ流体を押し出す。これらの①、②のシーケンスにより、ダイヤフラム内の流体は左から右へ移動する。③:左端のダイヤフラムが拡がることで、新たな流体を吸入する。④:中央のダイヤフラムが拡張することで、さらに吸入する。以上の①~④のシーケンスにより、流体制御ができる。また、ダイヤフラムの動作周期を変えることで、流体の流量制御が可能となる。MEMS内の左右2ブロックを機能的に動作させることで、2種類の液体の混合および分離制御が可能となる。
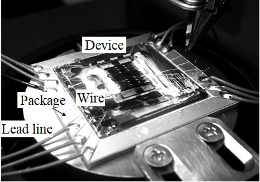
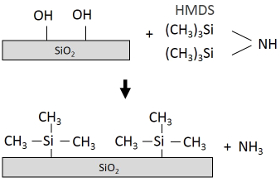
上の左図は、実際に作製し動作させた流体制御MEMSの写真を示している。デバイス形状は平坦的であり、コンパクトなパッケージングが可能である。制御用の配線も多数確認できる。この流体制御MEMSは、流体との接触面に高分子膜を適用しており、反応性および腐食性流体を取り扱うことができる。ここでは、上の右図のようなシランカップリングガスの制御について紹介する。シランカップリング剤としてHMDS(ヘキサメチルジシラザン)を用いる。通常、シランカップリング処理は、バブリングや気化器などでガス化し、N2などのキャリアガスで送流する。
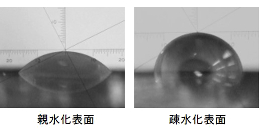
固体表面の濡れ性は、右図のように、純水の接触角として敏感にモニターすることが可能である。疎水化処理を行うことで、接触角は増大する。下図にはMEMSデバイスの流出口におけるガラス基板について、純水接触角にて評価した結果を示している。接触角が高いほど、疎水化処理が進んでいることを示している。時間の経過とともに、最初15度であった親水性表面が、流体制御MEMSによる処理により55度まで上昇し、疎水性ガスが導入されていることが明確である。このように、MEMSデバイスの中でも、コーティング技術は重要な役割をしている。今後も、単なる保護膜コーティングではなく、デバイスの構成要素の一つとして有効に機能させることができる。
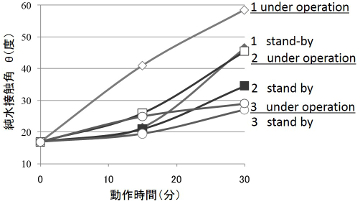
参考文献
- Akira Kawai, "Micro channel device composed by fry film resist, J. Photopolymer Science and Technology", 21, 43-46 (2008).
- Akira Kawai, "Fluid control MEMS composed with polymer materials", J. Photopolymer Science and Technology, in press (2011).
多層レジストプロセスの高機能化によるCu配線形成
デバイス構造特有の段差によって、パターン露光時の焦点深度のズレが原因となって様々な問題が生じる。その結果、配線パターンの線幅増大や, それに伴う配線抵抗の変化などを生じさせる。これらの段差部での寸法変動を改善するためには多層レジストプロセスが有効である。
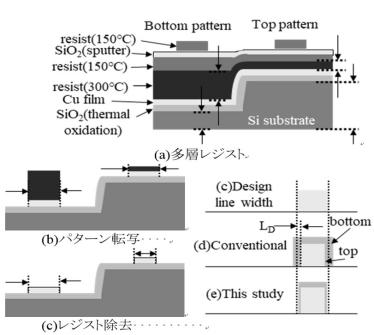
右図aに示すように、多層レジストプロセスでは、厚膜の下層レジストによって段差を平坦化することで、単層のプロセスと比べ露光時の焦点深度のズレを軽減できる。しかし、右図bのように、レジストの厚膜化により段差上下で膜厚変動が生じるため、段差上部の方が早くエッチングが完了する。そのため、右図cのように段差下部のエッチング中も、段差上部のパターンがプラズマに暴露され、右図dのように段差上部のパターン幅が細くなる問題が生じる。これを解決するため、下層レジストのベーキング温度を変えて、エッチング選択比を低下させることで、レジストサイドエッチングを発生させる。これにより右図eのように段差下部のサイドエッチング量を増加させ、配線の線幅を制御する。実験では、Si基板上にCF4ガスでのRIE(Reactive Ion Etching)によって段差を作製した。段差の深さは平滑化を想定して1μmとした。その上にSiO2熱酸化膜、Cu膜、下層レジスト(ベーキング:300℃)、下層レジスト(ベーキング:150℃)、SiO2スパッタ膜、下層レジスト(ベーキング:150℃)を形成する。その後、最上層のレジストに配線パターンをリソグラフィし、CF4, O2, ArガスでのRIE(reactive ion etching)によってCu配線を形成した。
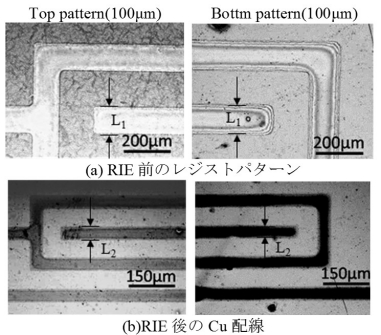
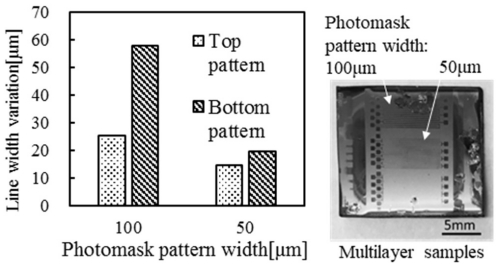
上図に、段差の上下部それぞれのRIE前後での拡大写真を示す。エッチング前の寸法をL1、エッチング後の寸法をL2とし、線幅の変化量をL1-L2として右図にまとめている。段差下部の方が段差上部に比べて、RIE前後の線幅変化量が大きい。これは、下層レジストによる平坦化の結果、段差下部のエッチング耐性の低いレジストの層が厚くなることで長時間エッチングされたためにサイドエッチングが多くなっている。その結果、Cu膜のRIE時にエッチングマスクとなる下層レジスト(ベーキング:300℃)が段差上部と比べて細ったことが原因でCu配線も細くなっている。本来、段差上部では段差下部に比べて下層レジストの膜厚が薄いため、より早くCu膜のエッチングが完了する。そして、その後もプラズマ下に曝されるためCu配線へサイドエッチングが発生し、段差上部では線幅が減少するはずである。しかし、実際には段差下部の方がエッチングによる線幅減少量が顕著である。すなわち、Cu配線へのサイドエッチング以上に、段差下部のレジストパターンのサイドエッチングによる線幅現象が大きくなる。
多層レジストを用いた際のオーバーエッチングによる線幅減少の改善には、下層レジストサイドエッチング量をコントロールすることが効果的である。これにより、段差部でのCu配線の寸法安定性の向上が実現できる。
ポジ型レジストを用いたネガパターン形成
既存のポジ型レジストを用いて、ネガパターンを形成することが可能である。必要な機器は、電子顕微鏡(SEM)による電子線描画と紫外線(i線)照射装置とホットプレートである。ここでは、ノボラック系ポジ型フォトレジストを使用した例を紹介する。下図に電子線照射/UV露光によるプロセスフローを示している。
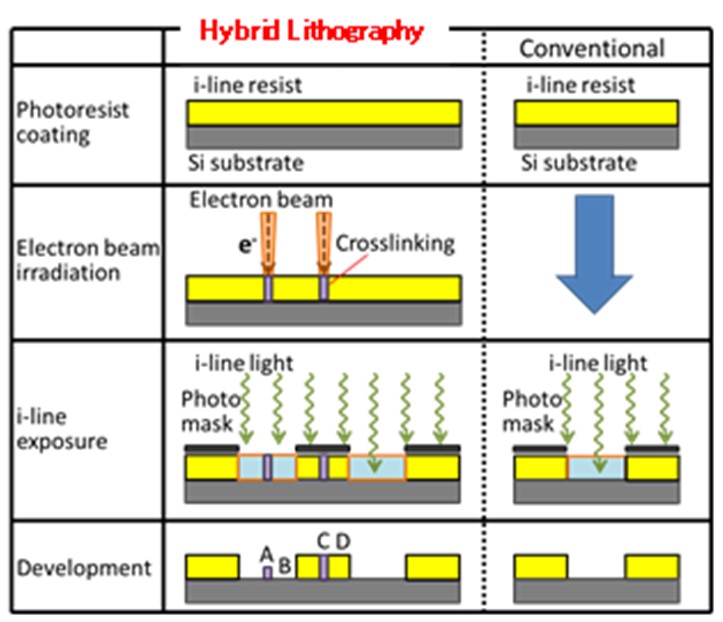
(ハイブリッドリソグラフィ)
[1]Si基板上へレジスト薄膜を形成して、プリベークを行う。
[2]レジスト膜に対してSEM等の電子線描画装置を用いて所望のパターンを描画する。この時、電子線照射部は電子ビームにより硬化が進み、アルカリ現像液には不溶化している。
[3]UV全面照射を行い、電子線描画の領域以外をアルカリ可溶にする。
[4]アルカリ現像液に浸漬することでUV照射部を溶解除去できる。
[5]ポストベークを行う。
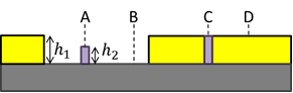
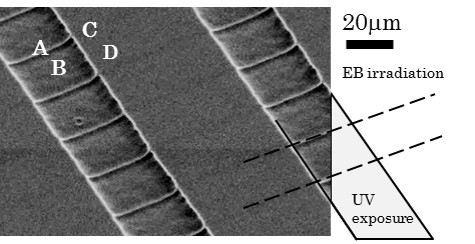
上の左図と右図には作成したパターン構造の断面図およびSEM写真を示している。UV露光により可溶性領域、電子線照射により難溶性領域を形成し、フォトレジスト膜内に混在させることで、ポジ型レジストを用いてネガ型パターンを実現していると考える。この電子線照射/UV露光を用いたハイブリッドリソグラフィは、ポジ型レジストの有効利用にも寄与すると考えられる。
3次元リソグラフィ(光造形法)による微小立体構造作成
長い年月を経て進化した生物の優れた機能や構造を模倣し、技術開発やモノづくりに活かそうとするバイオ・ミメティックスが注目されている。フジツボの外力から内蔵を護る殻の耐久性及び殻内の圧力を変化させることで海水を還流させることに注目した。ここでは、光造形法を用いて、3次元のフジツボ形状を模倣したデバイスを作製した。そして、作製したデバイスが触覚センサとしての機能を有し、液体を透過するフジツボ形状が変形しないことを検討するために熱変形実験及び外力変形のシミュレーション実験を行った。
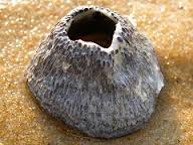
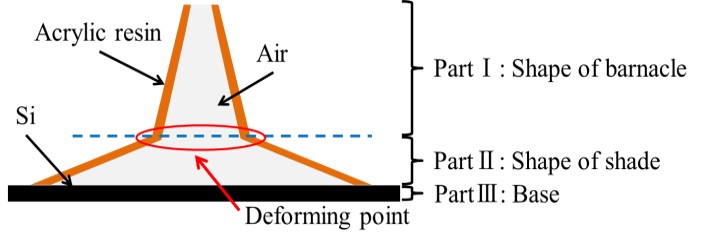
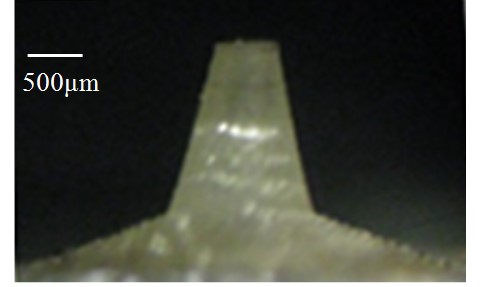
上の左図に示すフジツボの形状を模倣してデバイスを作製した。作製したデバイスを右図に示す。上の右図にデバイスの構造を示す。下の左図はマイクロ光造形装置を示す。下の右図にデバイスの設計図及び寸法を示す。構造はフジツボの形状を模倣した上部(上半径0.50mm, 下半径1.4mm, 高さ1.8mm,厚さ0.10mm)と、かさ状の下部(上半径1.4mm, 下半径5.0mm, 高さ0.7mm,厚さ0.10mm)で構成される。Si基板は有機洗浄を施した。マイクロ光造形装置(He-Cdレーザλ=345nm)を用いてSi基板上にアクリル樹脂のサンプルを造形した。造形後、デバイス内に残った造形液を取り除いた。
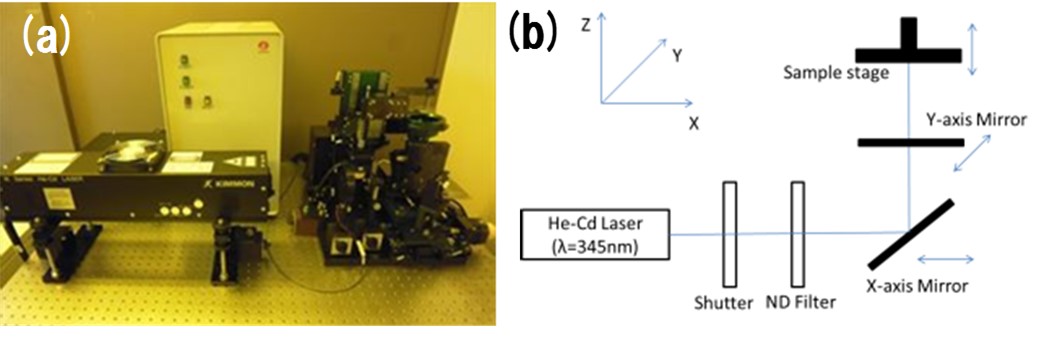
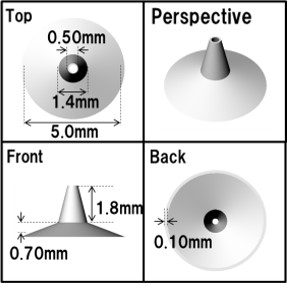
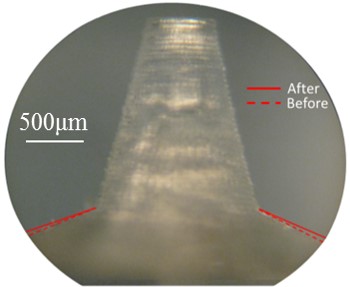
デバイスの加熱は、時間に対して温度を対数関数的に上昇させ、20分間行った。最高到達温度は220℃であった。加熱後、デバイスの温度が室温になるまで自然冷却させた。右図は実体顕微鏡によって観察した加熱前と加熱後冷却した写真を重ねたものを示す。右図より、デバイスは加熱によって、下部が下に沈み込み、上部の形状が変化しないことが確認できた。
サンプルの外力による変形のシミュレーションは、3次元有限要素法(FEM)を用いて行った。モデルの固定点はSi基板である。荷重条件は、モデルの側面に1[mN]の外力を加えた。下図に(a)は45°、(b)は0°、(c)は-45°の角度で側面に外力を加えた時のシミュレーション結果を示す。下図より、外力による変形は、サンプル上部の変形は小さく、下部は大きく変形することが確認できた。
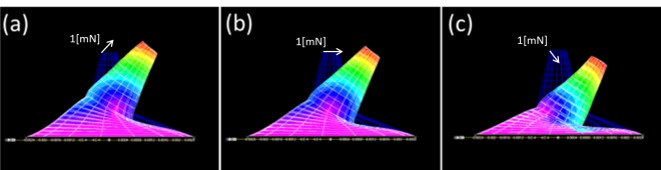
熱変形実験及び外力変形シミュレーション結果より、デバイスに応力が働くと体積が変化し、内圧が変化すると推測する。この内圧変化は触覚センサに応用できると考える。また、上部のフジツボ形状を維持することから、応力が働いても液体透過性を維持すると考える。本デバイスは、触覚及び発汗機能を有する人工皮膚などの応用が期待できる。